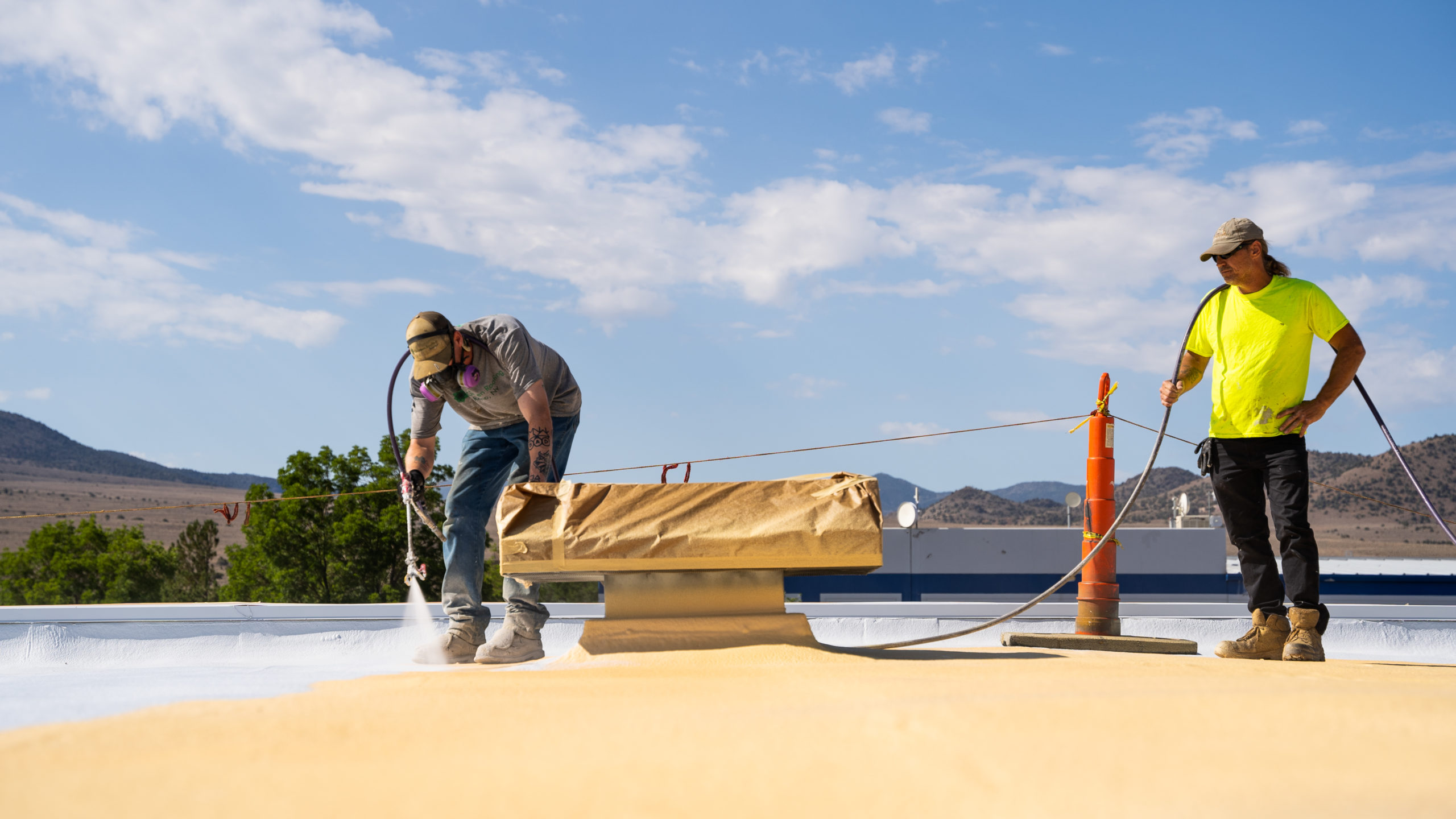
The Evolution of Roof Coatings Over The Years
Roof coatings are used for a wide range of applications, all over the world. Whether it’s for blocking UV radiation, protecting from leaks and storm damage, or for anything else, they’re gaining popularity—and for good reason.
Since they’re so advanced and widely used, it seems like roof coatings have been around forever. They’re a great investment, so much so that they seem like a no-brainer.
However, a lot of research and development has gone into turning them into what they are today. Let’s take a look at how they’ve changed over the years!
Early Stages
Liquid and spray roof coatings started to become widely used and developed in the 1960s.
Believe it or not, the very first roof coating was spray polyurethane foam, also called SPF for short. Though it’s not used as a topcoat today, it helped pave the way for other types of coatings.
Back in the 1960s, homes and business owners were looking for ways to protect their roofs from weather adversities. They wanted to make sure rain, snow, and storms wouldn’t result in water seeping into their structures.
Since it was great at sealing cracks and preventing leaks, people started to use SPF more and more. It was promising, but it had its major flaws.
The sun’s UV rays started to deteriorate the polyurethane material, making it an unstable and undesirable coating that didn’t last long in the elements.
After manufacturers and applicators noticed this, they decided to try experimenting with different materials to create coatings that would protect the spray polyurethane foam. This spawned a few different variations of roofing coatings.
Polyurethane Coatings
Polyurethane coatings started in the 1960s when they began as spray polyurethane foam. As we mentioned earlier, these spray foam coatings were sought after for their sealing capabilities, but they didn’t hold up well on their own against UV radiation.
This led to the development of acrylic and silicone roof coatings, as well as liquid versions of polyurethane coatings that were all designed to go on top of SPF roof systems.
The liquid version of polyurethane coatings had much better UV radiation resistance and kept the original sealing and weather protection properties their spray foam ancestors had.
Today, liquid polyurethane coatings (also known as polyurethane roof paint) are used for sealing a variety of different roofing materials, from modified bitumen to concrete and stone. They’re especially effective at providing impact resistance for foot traffic.
Polyurethane coatings come in two different forms: aromatic and aliphatic. What’s the difference?
Aromatic polyurethane coatings are applied to create a base layer and aren’t as UV stable as aliphatic coatings.
On the other hand, aliphatic coatings are applied as a topcoat and are more UV stable, holding up to more intense conditions than aromatic formulas.
Contractors should factor in the different types of polyurethane coatings when planning their projects. They should know which material will work best for creating impact protection and sealing off the substrate (aromatic) and which is best for providing heavy-duty UV protection (aliphatic).
Overall, polyurethane coatings are great for sealing, impact protection, and UV reflection, but they require a specific application process to make sure each layer does what it’s supposed to.
Acrylic
In the mid-1950s, acrylics technology advanced to the point where acrylics could be incorporated into liquid materials.
This led to the development of acrylic liquid products, with house paint being the most well-known. It was a thicker, more durable version of regular house paint that was a leading product for decades.
Acrylic house paint isn’t the same product as the roof coatings we see today, but the material’s technological advancements helped pave the way for them.
The roofing industry eventually developed acrylic polymers that were engineered specifically for roof applications.
Water resistance and harsh weather durability were some of the main draws towards using acrylic roof coverings. Like liquid polyurethane coatings, they were also developed to protect SPF roof systems.
The liquid acrylic materials provided great sealing properties and acted as a sort of “sunscreen” for existing roof coverings that couldn’t stand the UV rays themselves.
Today, acrylic coatings can last upwards of 15 years and can be easily applied using a paint roller and other simple equipment.
For the best installation results, they should not be applied in freezing temperatures or when precipitation (rain, snow, ice, dew) may occur within a specified period from the application.
The cure time of these products is dependent on weather conditions as well. Cold weather or high humidity will impede curing, so it’s ideal to apply them during periods with warm weather and low humidity.
Acrylic roof coatings continue to be sought after for their high level of protection against weather, UV rays, and moisture, while still being cost-effective and easy to apply.
Silicone
Similar to acrylic products, silicone roof coatings were designed to help protect spray polyurethane foam roof systems.
In the late ‘60s, manufacturers and applicators starting using silicone mixtures to seal off the SPF systems that weren’t holding up on their own in the sun.
Silicone roof coatings were developed through a lot of experimentation, eventually resulting in the high-solids product we’ve come to know. They held up great against UV rays, were incredibly adhesive, and were overall very promising products.
Today, silicone coatings are manufactured with high solids dispersion, meaning the material is about 96% made out of silicone solids.
This is part of what makes them so adhesive; they’re less likely to lose product over time due to evaporation. However, this can make applying them a bit more technical than their acrylic or polyurethane counterparts.
Silicone roof coatings are also highly elastic, meaning they won’t turn brittle and crack over their 20+ year service lives.
Overall, silicone roof coatings are great for providing long-term UV protection, sealing off leaks and moisture, and holding up through harsh weather conditions.
Rugged Coatings
Rugged Coatings was formed by industry veterans who were sick of supply chain and customer service issues resulting in difficult and unpredictable workflows for contractors and distributors.
At Rugged Coatings, we’re dedicated to providing durable silicone and acrylic elastomeric roof coatings that stand the test of time, backed by great customer service and reliable supply chain management.
We understand that you need a consistent partner to provide you with roof coatings where you need them, when you need them, without question.
Be the contractor or distributor that’s known for consistently great results. Partner with Rugged Coatings!
If you’re interested in getting our products or becoming a distributor, contact us!